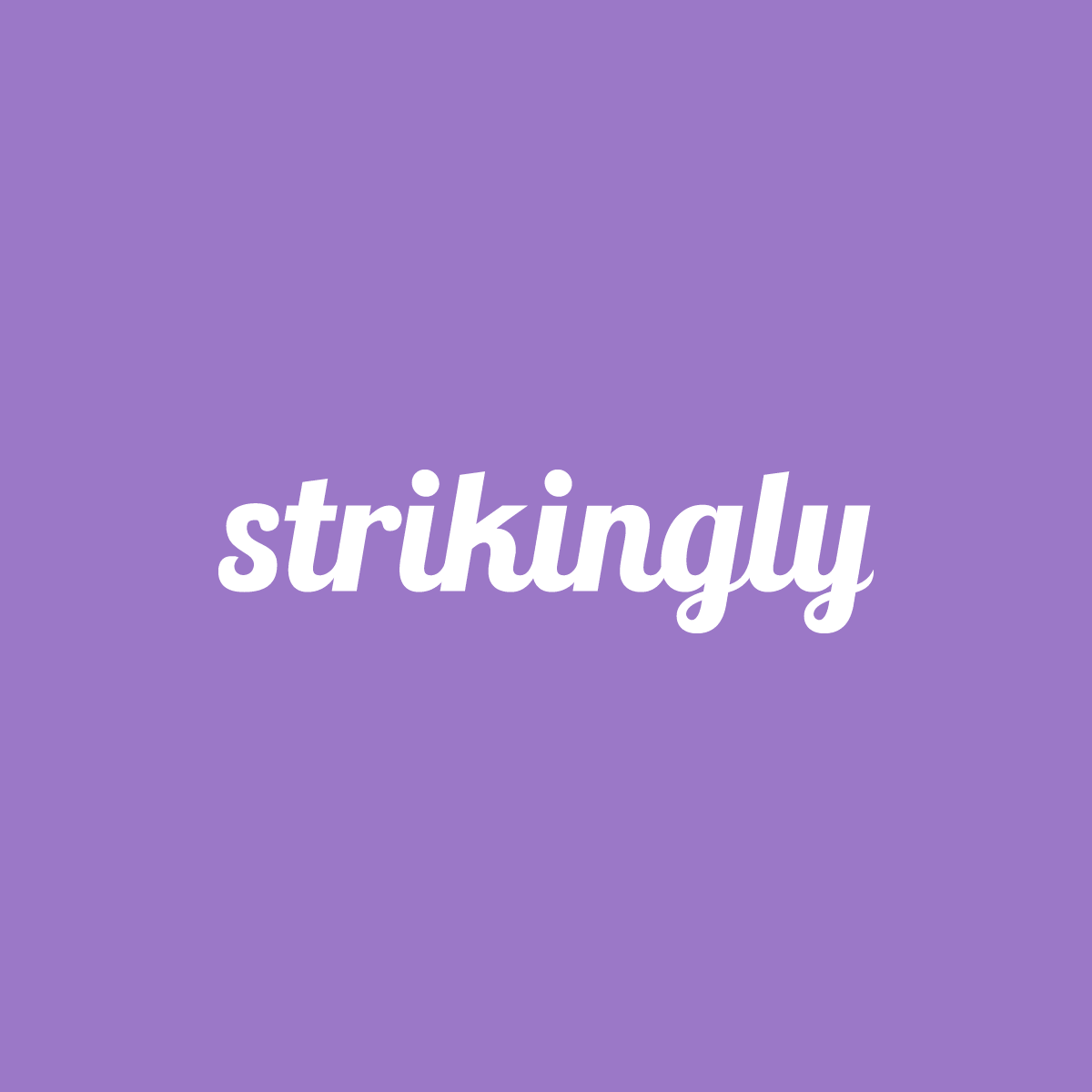
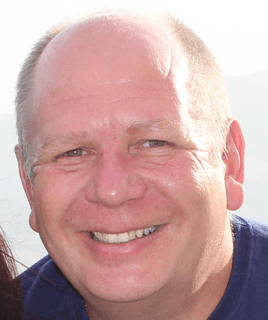
Global Steelplant solutions
Bob Williams
Steelmaking Consultant
About ME
I am an experienced manager with fifty years involvement in the steel industry. I have fulfilled numerous positions within the hierarchy of the Electric Arc meltshop management structure, including Steelmaking Supervisor, Shift Manager, Quality Manager, Operations Manager, Technical Manager, Plant Manager and most recently, Technical Director.
As a steelmaking supervisor, I have considerable experience making most grades of steel, from low grade constructional and rebar steels through the whole range of Stainless Steel and Special Steels.
I have worked for the leading steel mill equipment suppliers, namely SMS, Danieli, Siemens VAI, Sarralle, Inteco, Primetals and Tenova, where I have been involved with plant start-ups and commissioning of electric arc furnaces and secondary metallurgy units, (including ladle furnaces and degassing units). I have advised companies on best steelmaking practices to improve standards to be more competitive in world markets and I have compiled and conducted bespoke training programmes for Electric Arc Furnace, Ladle Furnace, Argon Oxygen Decarburiser, Vacuum Degassing and Ingot Teeming.
I have extensive experience with Direct Reduction Iron (DRI), Hot Briquetted Iron (HBI) and considerable experience of making stainless steel through the Argon Oxygen Decarburisation (AOD) route and with ingot teeming.
Recently I have been involved with several projects requiring extensive research in the reduction of CO2 emissions in the steel industry as demanded by the Paris Climate Agreement of 2015.
I have worked in many countries throughout the world including, Russia, Iran, USA, Egypt, South Korea, Saudi Arabia, China and Venezuela to name but a few.
I am currently available.
Please get in touch with me at: bobwilliams43@hotmail.com
with your requirements.
pROJECTS INVOLVED WITH INCLUDING:
IN MY LAST AND CURRENT POSITIONS, I HAVE FULFILLED THE ROLE OF COMMISSIONING MANAGER
I have just finished working as an SME - (Subject matter expert) for the electric arc furnace and steelmaking for fluor on their decarbonisation project witrh arcelormittal.
Recently i have been advising clients on the technology available for reducing CO2 output from the steel industry and for producing 'green steel'. (part time).
Technical Advisor for new meltshop projects in west africa and middle east. (part time).
rECENTLY SPENT NINE MONTHS AT the VALBRUNA SITE IN WELLAND, ONTARIO, CANADA, as an advisor/TECHNICAL ASSISTANCE FOR eaf, SECONDARY METALLURGY, CCM, AND INGOT TEEMING AND CONDUCTED A SERIES OF CLASSROOM TRAINING SESSIONS COVERING ALL AREAS.
start-up and commissioning.
ELECTRIC ARC FURNACE.
asia - including middle and far east
Hubei Shunle Stainless Steel Company (2 X Primetals Quantum Electric Arc Furnace)
POMINA STEEL, VIETNAM (cONSTEEL WITH HOT METAL)
LISHUI HUAHONG steel products, CHINA X2 (consteel)
TANGSHANG, CHINA (CONSTEEL).
hongtai steel x2 (CONSTEEL).
Taewoong Stainless and Special Steel, Busan, South Korea.
Midhani Special Steels, Hyderabad, India. (STAINLESS STEEL)
Krakatoa Steel. Indonesia. (HOT METAL, DRI AND SCRAP)
Zhongyuan Special Steels (ZYSCO), Jiyuan, China.
Yonggang Steel, China. (HOT METAL)
South Steel, Saudi Arabia. (DRI)
SULB, Bahrain. (DRI)Boashan Iron and Steel Company, China.
DONGBU, SOUTH KOREA. (CONSTEEL).
iRAN
IRANIAN alloy STEEL company - YAZD, IRAN.
saba 1 Esfahan, iran. (DRI)
SABA 2 ESFAHAN, IRAN. (DRI)
KHUZESTAN STEEL COMPANY, AHWAZ IRAN. (DRI)
usa and americas
Valbruna ASW. Welland, Canada. EAF, VORS, AOD. Technical Assistance/advisor.
JSW, USA 400T EAF with Consteel (Restart)
Charter Steel, Saukville, USA. (CONSTEEL).ICH, Rio Bravo, Mexico.
Republic Steel, Ohio, USA.
Sizuca Gerdau, Venezuela.
Nucor Memphis, USA.
North American Stainless, Ghent, Kentucky, USA. (Stainless Steel)
Europe/north africa
Ervin Amasteel, Dudley, West Midlands, ENGLAND.
ArcelorMittal Ostrava, Czech Republic
PNTZ, Pervouralsk, Russia.
Tagmet Steel Taganrog, Russia.
Halyvourgia Hellenic, Velestino, Greece.
OMK, Vyksa, Russia.
UMMC, Serov, Russia.
Arab Company for Special Steel – Arcosteel, Sadat City, Egypt.
SECONDARY METALLURGY
OVAKO, HOFORS, SWEDEN. VD
KARDEMIR, KARABUK, TURKEY. VD
TOSYALI, ISKENDERUN, TURKEY. 2xLF.
MKE, KIRIKKALE, TURKEY. VD
MIDHANI SPECIAL STEELS, HYDERABAD INDIA. LF, VOD.
ZHONGYUAN SPECIAL STEELS (ZYSCO) JIYUAN, CHINA. VD/VOD, LF, AOD.
KHUZESTAN STEEL COMPANY AHWAZ IRAN. VD.
KONIAMBO NICKEL, NEW CALEDONIA. LF.
ARCELORMITTAL OSTRAVA, CZECH REPUBLIC. LF, VD
DUFERCO, LA LOUVIERE, BELGIUM. VD
PEINER TRAGER, PEINE, GERMANY. VD
KOSCO, SOUTH KOREA. VD
DONGBU, SOUTH KOREA. LF, VD
OMK, VYKSA, RUSSIA. LF, VD
UMMC, SEROV RUSSIA. LF, VD
MECHEL STEEL, RUSSIA. LF, VD/VOD
CSH, CONSUMPCION, CHILE. VD
GERDAU AMERISTEEL, SAND SPRINGS, OKLAHOMA, USA, LF.
ARAB COMPANY FOR SPECIAL STEELS, SADAT CITY, EGYPT. LF, VD/VOD
SABA, ESFAHAN, IRAN. LF, VD.
NATIONAL IRANIAN STEEL COMPANY, (NISCO), YAZD, IRAN. LF VD/VOD.
COMMENDATIONS
Mr. Williams is a professional in anything he does. I had the honour to work with him in several projects around the world facing every time different challenges. Very target oriented he always accomplishes the required task making happy all its stakeholders. Any time I need help or I have doubt about steelmaking, from raw materials to finished product, I can rely on his hints.
Excellent for both on site activities and training / documentation issue. Read Robert’s technical report is as easy as to read as his novels.Michele Pustorino
Process, Operations and Assistance
TENOVA
Bob Williams worked with us to install and commission our equipment at customer TAEWOONG, South Korea. His positive attitude, work experience and perfect knowledge of our facilities were our great assets in this project and we very much appreciate them. I will use his knowledge and experience in the field of metallurgy in other projects, including input analysis and preparation of optimal metallurgical processes.
Martin Pavliš
Managing Director
INTECO PTI s.r.o.
Sms Concast's collaboration with bob williams was very proficient due to his long and broad experience in steelmaking
his educated knowledge of the steelmaking process gave a different perspective to our job and helped the team grow.
it goes without saying that he was able to master any difficult situation via a close and trusty relationship with his colleagues.
Marco VOLPE
SENIOR PROCESS ENGINEER
SMS CONCAST ITALIA
BOB WILLIAMS TAKES DELIGHT IN SHARING ALL HIS WORKING EXPERIENCES AND POSITIVELY TRIES TO FIND THE SOLUTIONS WHICH ARE MOST SUITABLE FOR OUR REAL SITUATION. HE IS OPEN-MINDED Yet HAS A CLEAR-CUT STANDPOINT. HE TALKS AND COMMUNICATES WITH EVERYONE FOR EVERY ISSUE FREELY. FROM HIM PEOPLE BECOME MORE LIKELY TO THINK BY THEMSELVES AND BRAVER TO SPEAK OUT THEIR OWN IDEAS ETC.
IN SHORT, BOB WILLIAMS WORKS RIGOROUSLY AND IS SERIOUSLY RESPONSIBLE FOR HIS WORK. HE HAS MADE A BIG CONTRIBUTION TO OUR COMPANY IN COMMISSIONING OF THE HIGH CLEANNESS STEEL PROJECT, SAFETY MANAGEMENT, PRODUCTION MANAGEMENT, STEEL QUALITY IMPROVEMENT ETC.
MR WANG
MANAGING DIRECTOR
ZHONGYAN STEEL COMPANY (ZYSCO)
(FULL REVIEW AVAILABLE ON REQUEST)
I worked together with Bob in Kosco plant in south Korea. The client has a problem with hair cracks in rolling mill. After analysis of full technological process, the cause was found in the meltshop (electric current of the stirrers). For me, according to his knowledge, experience and attitude, he is one of the best specialist for electric arc furnaces and secondary metallurgy units.
it was a pleasure to work with him.
Francisko luksa
site manager at sms siemag ag
Areas of SPECIALTY
TRAINING
'YOU CAN HAVE THE BEST EQUIPMENT AVAILABLE, BUT IF THE OPERATORS ARE NOT PROPERLY TRAINED TO OPERATE IT, ITS ALL FOR NOUGHT.'
PLANT COMMISSIONING
ELECTRIC ARC FURNACE, LADLE FURNACE, VACUUM DEGASSING UNITS.
TECHNICAL ASSISTANCE
QUALITY ISSUES, CLEAN STEEL PRACTICES, SLAG CONDITIONING, POOR ELECTRODE CONSUMPTION, POOR REFRACTORY CONSUMPTION.
NEW PLANT ADVISOR
IF YOU ARE PLANNING TO BUILD A NEW STEELPLANT, I HAVE BEEN INVOLVED WITH THE STARTUP AND COMMISSIONING OF MORE THAN THIRTY EAF'S AND A SIMILAR NUMBER OF SECONDARY METALLURGY UNITS - I CAN HELP.
reach out
I'm available for work anywhere in the world.
Publications
Challenges for the Electric Arc Steelmaker in the 21st century. (Posted on LinkedIn)
Wootz Steel (Posted on LinkedIn 12/11/2021)
In 1899, the first commercial steel was tapped from an Electric Arc Furnace in Normandy, France, developed by Paul Héroult.Héroult was not the archetypal scientist, but someone who loved to travel, loved sport and the company of women, it is said, and his inventions came ‘out of the blue’, rather than from hours spent in a laboratory.Of course, the Electric Arc Furnace of 1899 looked nothing like a modern ‘state of the art’ furnace of today, but from the turn of the century until the 1960s saw little significant development of the electric arc process; since the 1960’s the development of this process was spectacular.The introduction of long and short arcs, oxygen injection, water cooled panels, ladle metallurgy, foamy slag, scrap preheating and bottom tapping were just some of the new technologies established to make the Electric Arc Furnace the efficient steel producer we see today.Now, the Electric Arc Furnace process faces another significant development.The Electric Arc Furnace route currently produces around 30% of the world’s total output of steel, but this figure is about to increase significantly, with some commentators suggesting that by 2050 this figure will be close to 100%!Why? And is this figure realistic?As the steel demand continues to grow - by 2050, it is predicted global steel output will exceed 2500 million tonnes, compared to 2020 where global output was 1800 million tonnes, so has the demand for ‘cleaner’ steel, as 197 countries agreed to commit to reducing the 40 billion tonnes of CO2 emissions we are currently pumping into the atmosphere, as part of the Paris Climate Agreement of 2015.Steelmaking and ironmaking account for 7-9% of the world’s CO2 emissions, with the Blast Furnace route responsible for 92% of this figure and the Electric Arc Furnace route just 8%.(BF/BOF 1.6-2.0kgs of CO2/kg of steel, DRI/EAF 1.1-1.2kgs CO2/kg of steel).Considerable developments are occurring at this time to reduce our industry’s carbon footprint, but most of the developments are with the Electric Arc Furnace process rather than with Blast Furnace.Green Hydrogen is the fuel that will lead the steel industry into a cleaner, eventually CO2 neutral future.However, the availability of Green Hydrogen will limit the advancement of the initiatives currently being undertaken by many of the world’s major steelmakers.In 2017, 96% of the global hydrogen production was from natural gas, oil and coal (grey hydrogen), and just 4% from the green electrolysis process. All of this production was consumed by the producer on-site – none was traded, sold or shipped.H2 DRIThe use of DRI in the Electric Arc Furnace has increased significantly over the past twenty years or so, with around 100 million tonnes being produced annually through the Midrex and Hyl (now EnergIron) processes.These processes were particularly popular in the Middle East, where scrap metal was, and still is, a rare commodity and where cheap Natural Gas is readily available.Due to regulations to be imposed over the coming years on CO2 emissions, pilot plants using hydrogen as the reductant gas rather than natural gas have been set up throughout Europe, which is taking the lead in this new development, though other countries have also initiated similar projects.However, with demand for quality ores for the DRI increasing, the availability of this ‘high-grade ore’ has decreased, leaving low-quality ores that produce a DRI of low ‘metalization, which makes the material less attractive to the steelmaker, because of, not least, the increased power requirement, (kWh/t) and extra gangue.Challenges facing the SteelmakerCurrently, the Electric Arc Steelmaking Process is dependent on carbon as a fuel, as >30% of the energy used to melt the steel comes from chemical energy. The carbon source is pig iron, hot metal, where the carbon content is around 4-5%, DRI or HBI, where carbon content is 1.5 – 2.5% or coal charged directly into the furnace.The furnace is also injected with carbon to encourage foamy slag - essential for good electric arc furnace operation, and achieved by the formation of CO that passes through the slag and makes it ‘foam’. However, achieving a good foamy slag requires a bath carbon content of 0.15-0.30%.With the new developments with DRI with green hydrogen, the carbon content of the DRI will be zero, so where does the carbon come from? Pig iron from the blast furnace?However, this problem is not insurmountable, as other developments alongside the Green Hydrogen DRI projects are happening. For example, in Australia, OneSteel has developed the Polymer Injection Technology, where recycled polymers, such as old car tyres, which would otherwise be sent to landfill, are mixed with some coke/anthracite injected into the furnace.Another process developed in the early 2000s was the Carbofer process, where baghouse dust was mixed with oily mill scale, lime and some carbon and injected back into the furnace.This process also produced a good foamy slag and reduced landfill costs. Oily mill scale and baghouse dust would usually be sent to landfill, and this process increased the zinc content of the baghouse dust to levels where it was commercially viable to recover the zinc from the dust.For whatever reason, the Carbofer process did not take off – maybe now is the time to revisit the Carbofer process!With an absence of carbon in the charge material, there will therefore be no ‘carbon boil’, which occurs when ‘cold’ carbon-bearing material enters the molten bath. This reaction is essential for nitrogen and hydrogen evolving from the melt.There is no doubt that using zero carbon DRI requires a complete rethink regarding the Electric Arc Furnace Standard Operating Practice. This was proven at North Star Steel Texas operation when they processed Circored Trinidad’s zero carbon HBI in the early 2000s.The results indicate that more electrical energy, C injection, and pig iron are required to melt zero-carbon DRI/HBI.The results of global warming are clear for all to see; as I write, 154 wildfires are raging across Greece, where I have made my home, with the USA, Turkey and Algeria, just some of the countries battling record temperatures and wildfires.We need to act – let us hope we’re not too late. We need another Paul Héroult.Bob WilliamsGreece 10/08/2021WOOTZ STEEL
What is Wootz steel?
A few months ago, I was working in Turkey and stayed in the ancient town of Tarsus. It was a short stay, and where I had the pleasure of meeting Jerry Wolfe, of PRI, with whom I spent an enjoyable week.
Tarsus' history goes back thousands of years and is the birthplace of Paul the Apostle. Apart from appreciating the places of archaeological and historical interest, we enjoyed walking through the bazaar close to our hotel. There were also several craft shops where we would watch the local artisans at work. One of these shops was of particular interest to Jerry.
Jerry is a specialist in heat treatment and has a forge. One of the artisans also had a forge and was making knives; Jerry asked if he had made knives from Wootz steel, and though the craftsman spoke little English produced a fine knife made from Wootz steel.
The mention of Wootz Steel piqued my interest, as it plays a significant part in one of my books; The Blacksmith's Sons (available at Lulu.com), and I had researched the origins of Wootz steel some years earlier, though, until this point, I had never actually seen any.
We each asked the knifemaker to make a similar knife for us, and he assured us they would be ready by the time we were due to leave. Mine is the one in the background.
The Origins of Wootz Steel.
Wootz steel was in high demand in the Middle Ages, especially for swords used by knights. Blades made from Wootz Steel were harder than the standard-issue swords, which were brittle and would often shatter into pieces if struck by a sword made from Wootz Steel.
However, the origins of Wootz Steel go back much further than the Middle Ages.
When Wootz Steel was first invented is unclear, it is known to have originated in India, and there is archaeological evidence of steel production in Tamil Nadu in around 300BC. The oldest literary records mention the steel during Alexander the Great's time in India in the 4th century BC.
The Indians were very secretive regarding the production of this high-grade steel, which was very much in demand.
It is made using the Crucible process, where an iron source, probably wrought iron, was placed in a crucible, in ancient times made of clay, along with a carbon source, wood chips. The crucible was then placed in a furnace, and as the temperature increased, up to around 1400°C, the carbon was absorbed into the iron, to between 1.2-2.0%, which would lower the steel's melting point liquify and be poured into ingots. The Wootz Steel was then ready for working or export to Rome or China in ingot form.
As I mentioned Wootz Steel was popular in the Middle Ages. The Crusaders came across it in the Holy land, when facing Saladin's Muslim warriors. Their impressive, curved swords were made from what they called Damascus Steel, likely imported Wootz Steel, from India or Ceylon.
© 2019